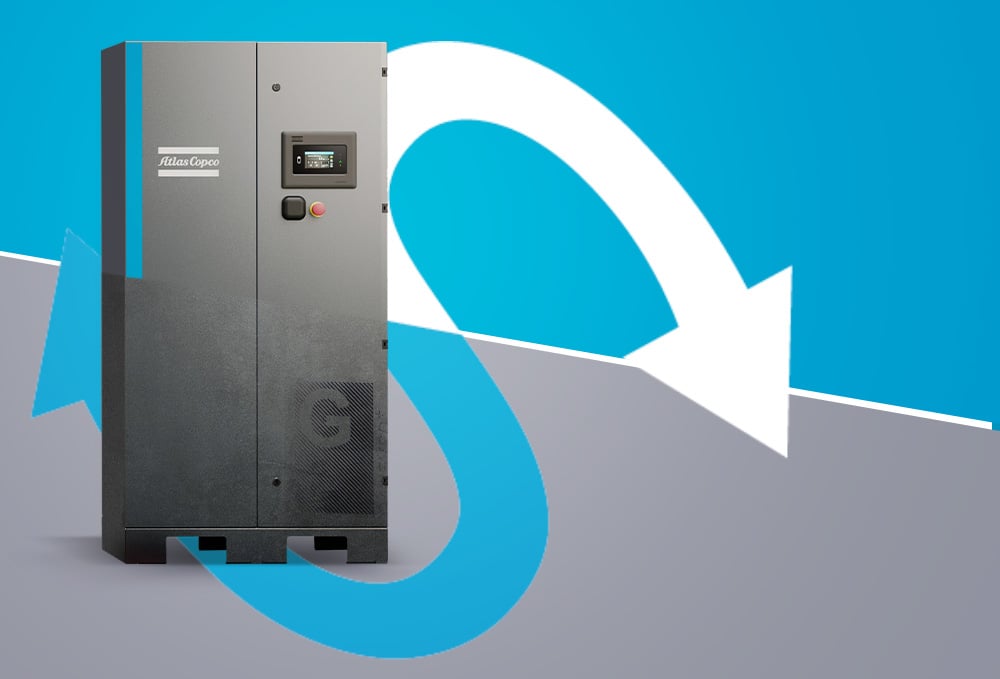
Oil-Injected Air Compressors
Imagine you are driving your car on a hot day. Your dashboard indicates you are low on oil and need an oil change. Your engine is running hot. You change the oil, which gets filtered through your car engine and cools the vehicle down. The car runs smoother because the oil is lubricating the engine and making everything run more efficiently and reliably.
Now think of a rectangular air compressor device, about six feet high and five feet wide, inside a furniture manufacturing facility. Using oil to lubricate the air compressor motor within that facility will make the manufacturing process run efficiently and smoothly. The air, which gets hot when compressed, won’t overheat because the oil will keep it cool. The compressor will function well because the oil will keep the engine lubricated and running efficiently so the furniture-making process progresses accurately and efficiently while minimizing energy consumption and accelerates the manufacturing environment.
This is an example of an oil-injected air compressor application! These machines are absolutely essential in powering a large variety of applications and industries - many of which wouldn't function without oil-injected compressors.