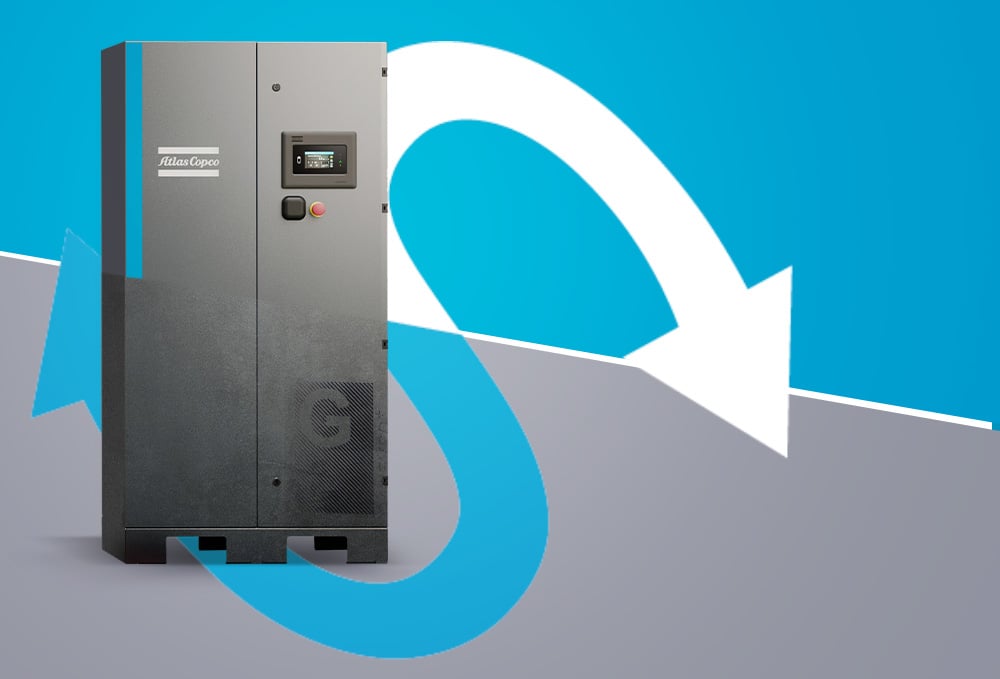
Air Treatment Overview
In many industries, compressed air requires additional air treatment once compression has occurred. There are a variety of ancillary compressed air products that assist in treating your compressed air, including air dryers, filters, drains, water separators, air receivers, and aftercoolers. Our air treatment guide runs through these ancillary products that can be used for treating your compressed air.