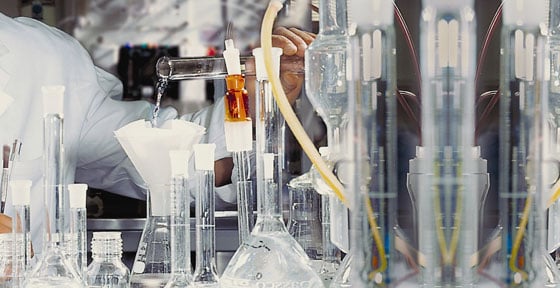
Don’t let the title scare you. We won’t get into the molecular structures of compressor lubricants on this blog (at least not today). Rather, we’d like to talk about the chemical properties that make lubricants a vital part of your compressor system.
Proper compressor maintenance includes replenishing lubricants with fluids that are engineered for optimal performance in their dedicated functions. For instance, if you work in the food and beverage industry and operate an oil-injected screw compressor, replenishing the lubricant with a non-food grade fluid could result in contamination and costly product recalls. Additionally, choosing poorly performing lubricants can lead to lower cooling efficiency, poor stability and insufficient protection, which could damage internal components.
The correct lubricant will optimize the performance of a compressor, resulting in a longer life at a low operating cost. The real chemistry is in the lubricant additives, which support base lubrication requirements and interact in multiple processes within the compressor. With the proper blend of chemical additives, a high quality lubricant can operate for thousands of hours at optimal performance levels.
The following properties or additives should be present in a high quality compressor lubricant:
- Demulsification or detergent properties facilitate the water-oil separation in the internal circuit and efficiently remove the condensate to decrease external pollution. This is especially important when operating in a dusty or aggressive environment.
- Anti-foaming properties efficiently separate air from the lubricant by maintaining a lubrication film. This results in lower oil carry-over and reduced contamination.
- Anti-wear additives protect the metallic surface against wear under high loads.
- Air release additives facilitate air separation to reduce oxidation within the lubricant. Reducing oxidation results in longer drain intervals even under heavy duty conditions.
High quality compressor lubricants result in a longer operating life for your compressor while extending the time between service calls. And more time between service calls means more money on your bottom line.
Atlas Copco offers a full line of compressor lubricants to meet your compressor’s unique operating needs. Contact your service representative or drop us a line for more information.