Editor's Note: This post was originally published in 2017 and has been completely updated for accuracy, comprehensiveness, and new information.
When it comes to compressed air systems, pressure and flow are two of the most common terms you’re sure to encounter. This is true whether you’ve just started your research into air compressors or have made the decision to request a quote from a compressed air provider! Pressure and flow are key measurements for compressed air systems, given that they help facilities size their compressors to power applications with the proper air volume and flow rate so that no energy is wasted.
What is Pressure?
Pressure is the measure of force that’s applied to an area and determines the compressor’s ability to perform a specified amount of work at any given point in time. The compressor must provide the right amount of pressure, or force, needed to complete the process. Too little pressure means the job won’t get done, whereas too much pressure can damage the equipment and cause unexpected malfunctions.
How is Pressure Measured?
Pressure is measured in pounds per square inch (psi). For example, 50 psi would mean that there is 50 pounds of pressure being applied per square inch. To check the PSI of your existing system, look at the air gauge on the air compressor – this is where the system pressure will be displayed.
What is Flow?
Flow is measure of volume that indicates your compressor systems output rate; it’s also considered to be your compressor’s ability to continue performing a certain task. The amount of flow needed depends on the length of time required to complete the task. With insufficient flow, the compressor will require breaks to rebuild pressure in the compressor’s reserve tank.
How is Flow Measured?
Flow is measured in cubic feet per minute (cfm) at a specific pressure and increases in direct proportion to the horsepower (HP) that is applied. So, when comparing a small compressor sold at home improvement stores to an industrial compressor located at a large manufacturing facility, it’s easy to see why the industrial compressor can achieve a much higher CFM than the smaller, at-home compressor.
Get more information on HP, CFM, and PSI here.
How Do Pressure and Flow Work Together?
Now that we know what these compressor measurements mean, let’s look at the relationship between them. The goal is to supply an application with the proper air flow (CFM) at the correct pressure (PSI). Say we need to move a 10 lb. block across a long table. While 100 psi of air pressure may not be enough force to move the block, 115 psi will, which is why it’s important to know the minimum pressure needed for your process. Blindly increasing pressure can cause an unnecessary increase in energy consumption. Simply increasing pressure by 2 psi causes a 1 percent increase in the energy needed to maintain the same airflow.
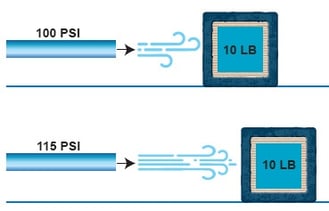
Airflow takes into consideration how often you need to move the 10 lb. block across the table. If the block only needs to move a small distance every hour, then a small compressor with a small air tank can meet those demands. However, if your application requires that you keep the block constantly moving over a span of many hours then you’ll need a larger compressor with more continuous flow.
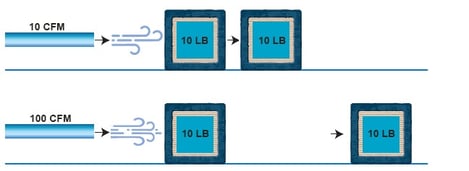
Beware of Overpressurization
One thing to keep an eye out for? Overpressurizing your compressed air system! Having a solid grasp on your application’s required pressure and flow can be difficult, which means many times facilities will overpressurize; this means that they will increase the system’s pressure (PSI) in order to make sure processes run consistently. Doing this, however, results in severe energy losses and high energy costs.
The Takeaway
Understanding pressure and flow will help you size your compressor based on process demands while reducing energy requirements, improving productivity, and lowering lifecycle costs. Not quite sure how to determine your system’s specifications? We recommend starting with a compressed air audit or reaching out to your local compressed air expert. We’re always available at www.atlascopco.com/air-usa!